Question:
"Why do watches have rubies in
them?"
Eleanor Hawkins, Lancaster, England
Answer by Professor J.C. Nicolet
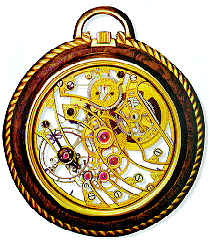
TECHNICAL REASONS
The important parts of a mechanical watch are mainly those that move, i.e. gear trains,
the balance and the escapement. In early times, the fine pivots of these pieces turned
directly in holes drilled into two brass plates separated by pillars. In order to
facilitate assembly and repair, the upper plate was later replaced by separate elements,
called "bars" (also "bridges" or "cocks" depending on the
number of supports).
The lower brass plate (called "bottom plate") was drilled with small holes in
which the other ends of the pivots turned. These holes also contained small oil sinks from
which the oil flowed into the holes to lubricate the pivots. With time, though, dust from
the air collected in the oil sinks. This resulting mix of oil and dust formed an abrasive
substance which acted like sandpaper, slowly filing away the softer brass of the plate and
to some extent even the harder steel pivots. With continued use, the abrasive action of
the oil-dust mixture working in concert with the turning action of the pivots caused the
holes to become oval. The watch would then start to work erratically, finally stopping.
These observations led watchmakers to look for a material harder than brass that would
withstand more wear and tear from the pivots. The substance they turned to was the ruby, a
material second only to the diamond in hardness.
A BIT OF HISTORY
The use of the ruby goes back to 18th century England (at the time the cradle of
quality horology) where watchmakers first had the idea of using small ruby pellets (called
jewels) as bearings for the pivots of the balance. The technique of drilling the ruby was
invented by a Swiss optician and astronomer, Nicolas Fatio, who went to England in the
hope of exploiting his invention. He tried to obtain a "royal privilege" for his
technique which they wrongly claimed was already in use. In the end, Fatio did not receive
the privilege and other skillful workers set about producing drilled ruby pellets for the
watch trade.
In those days stones were second-rate rejects from the jewelry trade. The technique
allowing fro precision drilling of the rubies gave the British watch industry supremacy
over continental horology for about 20 years. After that, French watchmakers such as
Abraham-Louis Breguet brought over English craftsmen (and their jeweling techniques to
work for them in France. This market the beginning of the end of the British monopoly.
For many years, this relatively costly labor-intensive technique limited jewels
exclusively to very high quality watches. Slowly their manufacture became more industrial
and their pieces more accessible to other aspects of watchmaking.
000
Making Synthetic Rubies:
Top- The creation of the elongated pear-shaped pieces of artificial crystal.
Bottom - The pear-shaped pieces are sliced using a copper and diamond cutting tool. The
slices are then cut into half, in squares and finally in rounds measuring from 0.3 to 0.5
mm in thickness and 1.15 to 2.55 mm in diameter. |
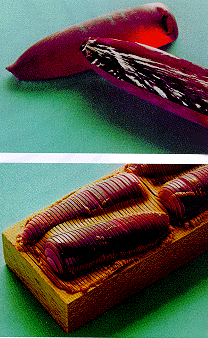 |
000
SYNTHETIC RUBIES
A further decrease in price accompanied the creation of synthetic
rubies, based a method developed in 1902 by August Verneuil, Professor in Paris'
Conservatoire des Arts et Métiers. In fact, synthetic rubies, as well as their natural
counterparts are corundum, i.e. crystal-line aluminum oxide.
In the industrial fabrication process, the basic component alumina (aluminum oxide)
undergoes a series of operations, i.e. purification, heating, fusion and crystallization,
which results in pear-shaped pieces of artificial ruby. Chromium oxide is added to get the
red color of natural rubies.
The large-scale manufacture of rubies permitted the creation of abundant quantities of
these synthetic stones, more homogeneous in quality than the ones found in nature. The
jewelry trade takes most of these stones. In watchmaking, the cost of the rubies came
mostly from the labor needed to drill and set them, as the cost of the raw material was
relatively low. Having said this, it must be noted that from beginning to end-product,
about 90% of the ruby is destroyed, with only the remaining 10% usable for watches. Up
until 1930, the ruby pellets were jewelry-fitted into the brass, but later, the technique
of driving (pressing) them into the plates was adopted, thus lowering production costs
even more.
A COMMERCIAL GIMMICK?
In the mind of the public, the idea that watches contain jewels give them a certain
added prestige value. Manufacturers were quick to exploit this belief and started to add
unnecessary stones to increase the prices of their products. The term
"upjeweling" was an American term coined to refer to this dubious practice which
was fairly widespread in the U.S. at the time. It was finally abolished by the U.S.
Customs authorities who disallowed "upjeweled" imports from entering the
country. There are some, however, who suggest that their real motives may have been less
noble and that this was merely a kind of camouflage protectionism for the U.S. watch
industry.
Today, Swiss watchmakers no longer use this questionable practice and their
advertisement is not based on the number of jewels in a movement. The total number of
rubies, i.e. "jeweling", can vary. In a simple hand-wound mechanical watch, the
number of jewels varies from a minimum of 14 to a maximum of 19.
In automatic or complicated watches, where there are more moving parts, the number of
rubies is higher. Once in awhile, someone will hear a rumor that a what repairer has
stolen the rubies out of a watch and replaced them with brass bearings. This is a totally
baseless myth. For the watchmaker to remove the rubies and replace them with brass would
require a lot of effort and would certainly not be worth his time given that the jewels
cost only a few cents to buy.
To sum it all up, having jewels in a watch is certainly a factor that adds to its
overall quality. They are indispensable for the long-life and correct functioning of a
good quality watch. |